Chemicals are everywhere. Everything from the soap you used to shower this morning to the glue holding your desk together is a product of the chemical industry. But when you try to determine everything that falls under the chemicals umbrella, things can get complicated. From a high-level perspective, chemicals can be broken down into three categories[i]:
- Basic Chemicals – These include petrochemicals (derived from oils), polymers, and basic inorganics. Petrochemicals are derived from hydrocarbons in crude oil and gas that are converted into more useful hydrocarbons by processes such as cracking, isomerization, and reforming. The main use for petrochemicals is the manufacture of a wide range of polymers, commonly used in plastics and resins. Basic inorganics include chlorine, sodium hydroxide, sulfuric and nitric acids, and chemicals for fertilizers.
- Specialty Chemicals – These include chemicals for crop protection, paints, and dyes.
- Consumer Chemicals – These are sold directly to the public and include detergents and soaps.
Many of these products come from facilities that are simply massive. The Sadara Chemical Company in Saudi Arabia was named the world’s largest chemical complex in 2015. There are 26 manufacturing units inside the compound with the entire industrial park spanning 12-square kilometers or approximately 4.6 square miles. The BASF chemical complex in Ludwigshafen, Germany takes up an area of approximately 10-square kilometers, or 3.9 square miles. “The backbone of the Ludwigshafen production Verbund (network) is a dense network of around 200 production plants that are connected to each other by over 2,850 kilometers of pipelines.[ii] In many other cases, the size of the company is commonly presented by revenue, number of employees, and number of chemicals produced. Dow Chemical, headquartered in Midland, Michigan, produces more than 2,000 different products.
Gases in the Chemical Industry
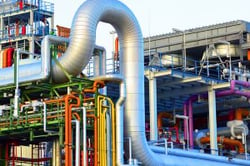
Within this giant conglomerate of chemical production, as well as the smaller producers, you are dealing with organic and inorganic hazardous materials that have very low flashpoints, low LELs (lower explosive limits) and a wide flammable/explosive range. LEL is the lowest concentration of a gas or vapor in air that will burn in the presence of an ignition source. For many flammable gases, it is less than 5% by volume. There is a high risk of explosion even when relatively small concentrations of the gas escape into the atmosphere. It is also worth considering that most flammable gas hazards occur when the concentration of gases or vapors exceeds 10,000ppm (1%) volume in air or higher. Toxic gases typically need to be detected in sub-100ppm (0.01%) volume levels to protect personnel. The production processes are complex, involving extremely high temperatures, pipelines and transfer lines, steam crackers, distillation processes, storage tanks, high pressure valves, turbines, concentrators, equipment connection points, and more.
Altogether, the production, storage, and distribution of products and byproducts of the chemical industry double as some of the most beneficial to consumer everyday lives, and some of the most dangerous to those who work with them directly. The contribution of gas detection management in the petrochemical industry therefore plays an imperative role.
Here are some tips on how to elevate your gas detection program within a chemical facility.
- Provide continuous gas monitoring – Personal gas monitors are a must, but continuous monitoring for LELs can alert you to a problem 24/7. Some area gas monitors have a 7-day run time that can be extended indefinitely with an external power supply. Area monitors are great for setting up a perimeter around a hazards area or monitoring a leak or spill.
- Keep workers connected – If someone experiences a man-down, panic, or high gas situation, it could take minutes or hours before anyone will know. With wireless gas monitors, peers in the area as well as a remote safety manager or first responder crew can be alerted immediately, improving response times.
- Use data to reduce and eliminate gas exposure – Gas detection management software helps you manage hazards, people, and equipment from anywhere with a simple dashboard. It also provides information on how gas detectors are being used, allowing you to take corrective actions.
You may be familiar with this quote by Sir Brian Appleton:
“Safety is not an intellectual exercise to keep us in work. It is a matter of life and death. It is the sum of our contributions to safety management that determines whether the people we work with live or die.”
In an industry as large and complex as the chemical industry, simply throwing a piece of safety equipment at a worker and sending him into a hazardous area is somewhat like putting on a seat belt and ignoring traffic rules and regulations. When it comes to your gas detection program, look for a comprehensive management solution to keep your workers safe.
[i] http://www.essentialchemicalindustry.org/the-chemical-industry/the-chemical-industry.html
[ii] https://chemicalparks.eu/parks/basf-se-ludwigshafen