In today’s industrial workplaces, connected safety solutions are revolutionizing the way we approach hazard detection and emergency response. The transition from traditional gas detection methods to advanced connected devices has given safety professionals unprecedented visibility into their sites. This real-time monitoring capability allows for proactive hazard prevention, significantly cutting down on workplace injuries and fatalities.
The Complexity of Connected Safety Programs
Implementing a connected safety program isn’t as simple as just deploying new devices. One of the primary challenges is ensuring reliable communication across the entire site. To achieve this, it's crucial to use a combination of cellular, Wi-Fi, satellite, and peer-to-peer networks. Redundancy is essential to avoid signal dead zones, which could result in missed alerts. For example, if a gas detector loses connection in a remote location, it could fail to relay critical hazard information, putting workers at risk.
While connected devices enhance awareness, they do not provide direct protection against hazards. These devices are designed to relay information about potential dangers, not eliminate them. Aggregating data from these devices allows safety teams to make smarter decisions and take preventive actions. However, this requires ongoing equipment maintenance to ensure reliability. A false sense of security can be dangerous, as it might lead workers to neglect necessary safety protocols.
Why Connected Safety Training is Critical for Security
The effectiveness of connected safety devices hinges on the actions taken in response to alerts. Alerts are meaningless if they are not acted upon appropriately. For instance, ignoring a man-down alarm can lead to preventable injuries or fatalities. It is essential that workers understand the importance of these alerts and respond promptly to ensure safety.
Several training gaps can also undermine the effectiveness of connected safety programs. Workers might misunderstand alerts, confusing calibration notifications with emergency alarms. Alarm fatigue is another issue, where frequent alarms lead workers to disregard them altogether. Additionally, there are missed opportunities for analyzing data patterns to identify and mitigate recurring hazards.
Implementing a Multi-Channel Communication Strategy
To maximize the effectiveness of connected safety devices, it's important to choose versatile devices that can communicate through multiple gateways, including Wi-Fi, cellular, and Bluetooth. Avoiding outdated technology that limits future updates ensures that the system remains adaptable and effective. Consulting with application engineers can help in scoping the appropriate gateways and pricing the solution upfront.
Effective communication strategies also involve customizing escalation plans for different types of emergencies. For instance, protocols should vary for man-down alarms, gas leaks, and other hazards. An example escalation plan might start with notifying a team lead and, depending on the severity, escalate to calling 911.
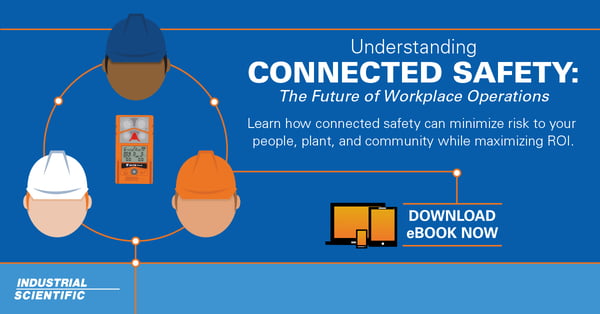
Best Practices for Connected Safety Training Programs
Training programs should be tailored to the specific roles and needs of workers. For example, confined space entry training is crucial for workers who frequently operate in such environments. Regular refresher courses are also important to prevent skill fade and ensure that workers remain proficient in using safety equipment.
However, training should be more than just a checkbox; it should be embedded in the culture of the organization. Encouraging workers to take alarms seriously and respond promptly is vital for maintaining a safe work environment. A culture of safety awareness ensures that everyone prioritizes safety and understands their role in maintaining it.
Maximizing Safety with Connected Systems and Training
In summary, connected safety solutions are only effective when combined with proper training and a multi-channel communication strategy. By integrating technology, comprehensive training, and reliable communication methods, organizations can create safer workplaces. Investing in connected safety training and reliable monitoring solutions is essential for proactive hazard prevention and emergency response. By doing so, companies can significantly enhance the safety and security of their work environments.