Confined spaces present unique dangers that workers must be prepared to handle. Despite tight regulations and technological advancements, permit-required confined space entry accidents and fatalities remain a problem.
According to OSHA, confined spaces are responsible for around 200 deaths every year and 60% of those deaths are workers who were attempting a rescue. What is the key to mitigating the risk of working in confined spaces?
In some cases, it could be as simple as reminding workers of acceptable and dangerous confined space gas levels. After all, low oxygen levels are the most frequent culprit of gas-related deaths in confined spaces.
Common Confined Space Gas Levels
Awareness of oxygen and combustible gas levels is essential for anyone tasked with entering a confined space, but those are not the only two confined space gas levels to be aware of; carbon monoxide and hydrogen sulfide are also common concerns. However, workers must understand the particular hazards of any environment they are entering and take appropriate measures by wearing a confined space monitor.
1. Oxygen
OSHA dictates that the minimum "safe level" of oxygen in a confined space is 19.5%, while the maximum "safe level" of oxygen in a confined space is 23.5%.
With low oxygen levels being the biggest cause of death in confined spaces, accurate oxygen level measurements are essential. Workers must sample the oxygen level prior to entering a confined space and should monitor it continuously throughout the work.
If a confined space's oxygen concentration surpasses 23.5%, the space is too oxygen-rich and could result in the ignition of combustible gases. On the other hand, low oxygen levels impair judgment and coordination. Extremely low levels of oxygen cause nausea, vomiting, and loss of consciousness.
When oxygen levels are too low, that typically means another gas is displacing it. In these instances, it’s important to know what gas is displacing oxygen and why.
2. Combustible Gases
Since gases cannot combust without enough oxygen, a confined space’s oxygen level can give you an idea of the concentration of combustible gases. There are two levels to pay attention to when measuring combustible gases:
- Lower Explosive Limit (LEL): This is the lowest concentration of a gas in the air that can combust or produce a flame when paired with an ignition source.
- Upper Explosive Limit (UEL): This is the highest concentration of a gas in the air that can combust or produce a flame when paired with an ignition source.
If a gas concentration is below its LEL, it cannot ignite, and the confined space is considered safe. If the gas concentration is above its UEL, the gas is too rich and there’s not enough oxygen for combustion.
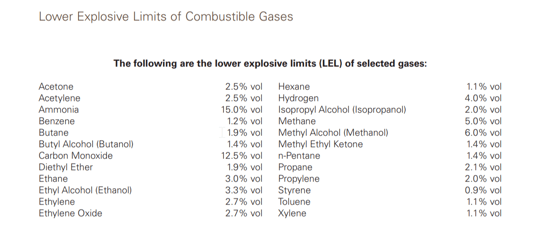
Of course, LEL and UEL differ for each gas. Methane, for example, has an LEL of 5% vol and a UEL of 15% vol. Methane combustion is possible when the gas level is at or above 5%, but below 15%.
Here is a list of common combustible gases and their lower explosive limits:
Gas detectors display a gas's presence as a percentage of its LEL. An atmosphere free of methane would show 0% LEL on the gas detector, but an atmosphere containing 5% methane would display 100% LEL.
It’s essential to be constantly aware of combustible gas levels while in confined spaces because they could change over time. A gas far above its UEL won’t ignite, but ventilation could dilute the gas and its concentration could quickly enter a combustible range.
3. Carbon Monoxide and Hydrogen Sulfide
Multi-gas monitors are frequently configured for carbon monoxide and hydrogen sulfide, but these two gases aren’t necessarily the most common in confined spaces. In fact, because carbon monoxide is the result of incomplete combustion, it’s uncommon in most confined spaces unless machinery is used inside.
While both of these gases are extremely toxic, confined space workers need to understand the hazardous gases they are most likely to encounter based on their specific application. Workers may be better protected by configuring their confined space monitor for other common gases.
It is still useful to be aware of the acceptable and dangerous levels of these gases. If carbon monoxide and hydrogen sulfide are gas hazards your workers could encounter, be sure they know the LEL/UEL for the hazards as well as OSHA’s permissible exposure limit (PEL) for each gas, which sets a limit on the amount of exposure for a worker within an 8-hour period.
Hydrogen sulfide has a PEL of 20 parts per million (PPM) and an LEL of 4.0%. Carbon monoxide has a PEL of 50 PPM and an LEL of 12.5%.
Keep in mind that permissible exposure limits can vary by jurisdiction, so the PELs OSHA lists for hydrogen sulfide and carbon monoxide are not universal.
The Importance of Direct-Reading Portable Gas Monitors in Confined Spaces
Gas hazards are unpredictable and confined spaces are dangerous, making it very important for confined space workers to continuously monitor gas levels with a direct-reading portable gas monitor. Direct-reading monitors not only tell workers whether the atmosphere in a confined space is safe, but also how safe. Is the oxygen concentration just barely above 19.5%, or is there enough margin to allow work to continue uninterrupted?
Safety laws require a pre-entry test just prior to a worker entering a confined space, and workers are only required to test again after leaving the space and preparing to reenter. Naturally, this leaves a lot of room for error if atmospheric conditions change while a worker is within the confined space, which is likely why confined space injuries and fatalities occur so frequently.
Periodic testing throughout the entry may be required if the confined space has a history of changing gas conditions, but “periodically” leaves room for interpretation by workers or the company. A safer procedure is to arm all confined space workers with direct-reading personal gas monitors and ask them to continuously monitor for gas hazards throughout the work period. If conditions begin to trend toward danger, workers will have the notice they need to exit the confined space safely.
If you rely on alarm-only monitors, this wouldn’t be possible. Because alarms are set to go off at predetermined thresholds, alarm-only instruments won’t give workers a heads up to potential dangers.
A direct-reading gas monitor, like the Ventis® Pro5, displays gas levels so workers can see the exact reading, allowing them to make more informed decisions about whether entry is a wise choice and whether they can continue their work safely.
Adding continuous monitoring to your confined space entry procedures is a simple way to improve worker safety. You can achieve continuous monitoring by asking workers to wear personal monitors on or by using an area monitor inside the space. You can improve safety even further by connecting personal monitors or area monitors to a hole watch via LENS® Wireless, enabling monitors to share gas readings and alarms so the attendant always knows exactly what’s happening within the confined space.